ASP integrated prefabricated pumping station
Category:Pumping Station
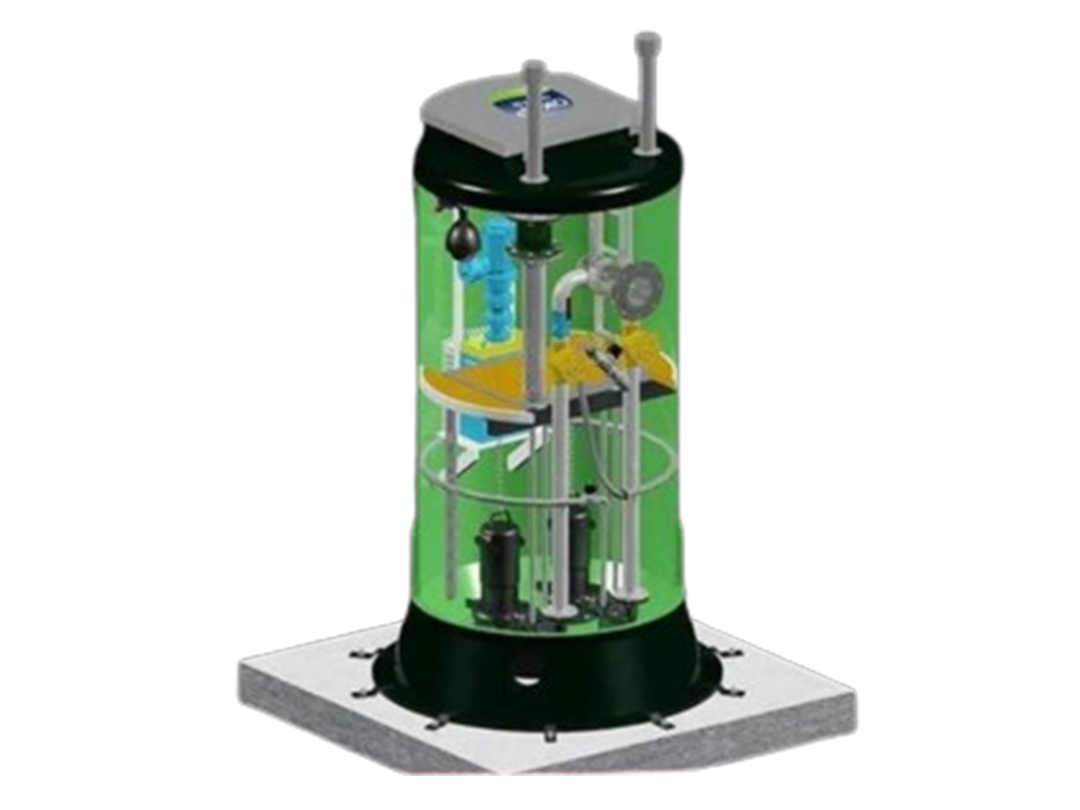
Product Details
Product Introduction
Wange Technology's integrated prefabricated pump station system develops solutions tailored to the specific environmental conditions of the project site, customizing prefabricated pump station equipment to reduce construction costs. From surveying, design, and production to pump pit excavation, installation, and testing, the process is quick, with installation completed within one or two weeks. It features a small footprint, compact equipment, and underground installation. The advanced management system enables remote control of the pump station. The fully intelligent control system allows for both on-site manual operation and remote monitoring via mobile devices (phones), eliminating the need for manual attendance. Its compact size belies its powerful functionality.
Applicable Fields
Suitable for areas where sewage cannot be drained by gravity alone. It collects wastewater below the sewer level through a wastewater channel, including wastewater far from municipal sewer networks and sanitation facilities, and then uses submersible pumps to transfer the wastewater to the sewer network.
Model Description and Meaning
Grating: T=Basket screen, F=Shredding screen
Number of Pumps: S=1 pump, D=2 pumps, T=3 pumps, T=4 pumps
Pump Station Height: 9.0=9.0 meters
Pump Station Diameter: A=1.2m, B=1.6m, C=2.0m, D=2.5m, E=3.0m, F=3.5m, G=3.8m, H=4.2m
Equipment Model
Configuration Table
Serial Number | Component | Standard Configuration |
1 | Tank | High-strength GRP fiberglass material, diameter 1.2m, 1.6m, 2.0m, 2.5m, 3.0m, 3.5m, 3.8m, 4.2m optional |
2 | Inspection Cover | GRP fiberglass or aluminum alloy material, non-slip |
3 | Handrail | SUS304 material |
4 | Ventilation Pipe | SUS304 material, optional deodorizing device |
5 | Safety Grating | Galvanized or SUS304 steel grating, matching the tank |
6 | Screen | Shredding screen or basket screen |
7 | Screen Guide Rail | SUS304 material, matching the screen |
8 | Screen Support | SUS304 |
9 | Inlet Pipe | SUS304 or fiberglass material |
10 | Inlet Flexible Joint | Galvanized flange, EPDM rubber, PN10 |
1 1 | Climbing Ladder | SUS304 material |
12 | Inspection Platform | SUS304+GRP grating, matching the tank |
13 | Liquid Level Gauge Protection Tube | SUS304 material, matching the sensor |
14 | Pressure Pipe | SUS304 material, double flange |
15 | Gate Valve | Soft seal, cast iron material PN10 |
16 | Check Valve | Wastewater dedicated, cast iron material, PN10 |
17 | Outlet Pipe | SUS304 or fiberglass material |
18 | Outlet Flexible Joint | Galvanized flange, EPDM rubber, PN10 |
19 | Submersible Sewage Pump | Non-clogging impeller |
20 | Coupling Base | Cast iron material, matching the pump |
21 | Guide Rail | SUS304 material, matching the coupler |
22 | Control Cabinet | Myuan-IC, manual/automatic control, remote alarm |
Product Features
● High integration of the integrated pump station system, small footprint, easy to achieve automation;
● The tank body uses advanced corrosion-resistant materials, reinforced fiberglass mechanical winding or special steel lining covered with fiberglass, with a long service life;
● The pump pit uses CFD fluid dynamics design, with good flow, no blockage, and self-cleaning function;
● The unique pre-swirl tank device can form a strong vortex at the bottom of the pump station, thereby achieving automatic cleaning, minimizing sludge at the bottom of the pump station;
● Reliable quality, no leakage, will not pollute the environment; light weight, low cost;
● Equipped with high-quality, high-performance submersible sewage pumps, widely used sensors constantly monitor the pump's operating status, greatly reducing maintenance costs;
● High degree of automation integration, allowing remote monitoring and unattended operation of the pump station
● Safe to use: Its scientific design and configuration greatly reduce the generation of highly toxic and odorous gases, protecting the environment;
● Fully buried installation, after installation does not affect the surrounding environment and landscape;
● Short installation cycle, saving most of the costs, maintenance is time-saving and labor-saving;
●One-time investment, low long-term operating costs, significant energy-saving benefits, and can be re-lifted and reused for secondary landfilling in case of demolition or land occupation;
●Fully customized, each time can design pump stations with different diameters and different heights of inlet and outlet pipe positions according to different projects, meeting the needs of various venues.
Fiberglass tank
Using fiberglass alkali-free coarse sand and unsaturated polyester resin continuous winding one-time molding cylinder (referred to as GRP cylinder), the cylinder thickness is uniform, the anti-extrusion pressure is strong, ensuring stable quality. 100% leak-proof test before leaving the factory to ensure no leakage.
The pump station cylinder uses fiberglass material with excellent physical properties, higher strength than steel and cast iron, with pressure resistance, corrosion resistance, and aging resistance. It has the advantages of long service life.
Fiberglass reinforcing ribs are added inside the cylinder, with reasonable spacing, which can increase the hoop strength of the pump station cylinder and prevent the cylinder from deformation or damage due to external pressure from the buried ground.
Performance Parameters Table
Performance Parameters Table | |||
Viscosity Pa.s | 0.30-0.60 | Elongation at break % | ≥2.2 |
Gel time min | 6-18 | Flexural strength Mpa | ≥105 |
Solid content % | 59-65 | Flexural modulus Mpa | ≥3300 |
Tensile strength Mpa | ≥55 | Heat deflection temperature ℃ | ≥60 |
Tensile modulus Mpa | ≥3500 | Barcol hardness | ≥42 |
Continuously wound reinforced fiberglass cylinder, computer-controlled winding process, ensuring uniform thickness and meeting design requirements, stable and excellent quality. |
Quick Installation Steps
![]() | ![]() |
Transport to site | Open Excavate |
![]() | ![]() |
Pipeline connection | Backfill and compact |
![]() | ![]() |
Electrical connection | Final debugging and document signing |
Pre-fabricated pump station selection table
Customer Information | User Name |
|
Project Contact |
| |
Project Name |
|
| |||
Installation Address |
| Contact Information |
| ||
Pump Station Design Basic Parameters | Ground elevation (m) |
| Daily pump station processing capacity (m3/d) |
| |
Inlet pipe bottom elevation (m) |
|
Single water pump Basic parameters | Flow rate (m3/h) |
| |
Outlet pipe center elevation (m) |
| Head (m) |
| ||
Inlet pipe diameter (mm) |
| Time change coefficient |
| ||
Outlet pipe diameter (mm) |
| Pump model |
| ||
Pump station type | Municipal sewage () |
Number of pumps | 1+1 backup () | ||
Municipal rainwater () | 2+1 backup () | ||||
Combined rain and sewage () | 3+1 backup () | ||||
Other () | Other () | ||||
Pump station components | Pump station inner diameter (mm) |
| Pump station height (mm) |
| |
Screen | Crushing screen ()Imported ()Domestic () Basket screen ()No screen ()Other () | ||||
Valve | Imported valve ()Domestic valve () | ||||
Pipeline material | Stainless steel 304 ()Other () | ||||
Service platform | Yes ()No | ||||
Control system | Float ()Static pressure level sensor ()Ultrasonic level sensor () | ||||
Automatic control ()Manual control ()Remote control () | |||||
Starting method | Direct Start() Soft Start( ) Frequency Conversion( ) Other () | ||||
Other Options | Axial Flow Fan( ) Plasma Deodorization( ) Hydrogen Sulfide Gas Detector( ) | ||||
Small Cantilever Crane( ) Stirrer Device( ) | |||||
Is valve well installation required? |
| ||||
Location of the electrical control cabinet |
| ||||
Other requirements |
|
KEY WORD:ASP integrated prefabricated pumping station
Related Products
Product Consultation
Leave your contact information to get a free product quote